Metal Bending Equipment: Essential Tools for Precision Fabrication
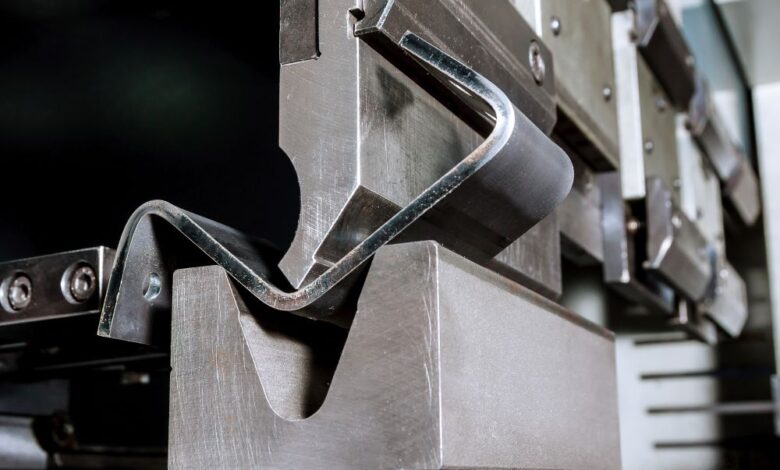
Metal bending equipment plays a crucial role in various industries, including manufacturing, construction, and automotive. It allows for precise shaping and manipulation of metal materials, enabling the creation of components that meet specific design requirements. Investing in the right metal bending equipment can significantly enhance productivity and reduce material waste.
Understanding the types of metal bending equipment available can help businesses make informed decisions. Options range from simple manual tools to advanced CNC machines, each with unique capabilities. Armed with the right knowledge, companies can select equipment that aligns with their operational needs and budget.
As industries continue to evolve, so do the technologies used in metal bending. Staying updated on the latest innovations can provide a competitive advantage, ensuring that businesses remain efficient and cost-effective. Embracing modern metal bending solutions can lead to improved product quality and faster turnaround times.
Types of Metal Bending Equipment
Various types of metal bending equipment are essential for shaping different types of metals. Each type offers unique features suited to specific applications.
Press Brakes
Press brakes are versatile machines widely used in metal fabrication. They consist of a upper ram that moves vertically and a lower bed where the sheet metal is placed. The bending take place when a tool and die combination is used along the length of the material.
Key features include:
- Precision: Capable of producing accurate angles and curves.
- Various Sizes: Available in different tonnages and lengths to accommodate various projects.
- CNC Options: Many models offer computer numerical control for automated bending processes.
Press brakes can be used for diverse materials including aluminum, steel, and stainless steel.
Tube Benders
Tube benders are specialized machines designed for bending tubular materials. They are essential in industries like automotive and construction, where bent tubes are used for frames and supports.
There are several bending methods, such as:
- Mandrel Bending: Maintains the tube’s internal diameter by supporting it during the bend.
- Rotary Bending: Utilizes a rotating die to bend the material accurately.
Features to consider include:
- Bend Radius Options: A variety of bend radius settings to meet design specifications.
- Manual vs. Hydraulic: Options range from manual models for small projects to hydraulic machines for high-volume production.
Sheet Metal Folders
Sheet metal folders are designed for bending sheet metal into desired angles without creating a crease. They are particularly useful for producing flanges and ducts.
Key components include:
- Adjustable Clamps: Secure material during the bending process.
- Variety of Bending Angles: Easily set for multiple angles for different applications.
Benefits of sheet metal folders:
- User-friendly: Typically easier to operate than other machines.
- Compact Design: Suitable for smaller workshops with limited space.
These machines enhance efficiency in tasks that require high precision.
Selecting the Right Equipment
Choosing the appropriate metal bending equipment requires careful consideration of several crucial factors. Each aspect influences not only the quality of the bend but also overall efficiency and operational costs.
Material Compatibility
Understanding material compatibility is essential when selecting bending equipment. Different metals, such as steel, aluminum, or copper, require distinct approaches for effective bending.
- Steel: Often requires significant force and high-quality tooling.
- Aluminum: More malleable, allowing for easier bends but may need special tooling to prevent damage.
- Copper: Requires careful handling to avoid cracking.
Equipment specifications should explicitly state which materials can be processed to maintain efficiency and avoid complications.
Bending Capacity
Bending capacity defines the thickness and width of materials the equipment can handle. It varies widely among machines, making it critical to identify specific project requirements.
- Thickness Ratings: Machines have limits based on the material type, often ranging from 1/16” to several inches depending on the model.
- Width Adjustments: Consider how wide the material can be for bending without losing precision.
Checking the manufacturer’s guidelines on bending limits ensures that equipment can perform required tasks without risk of damage or failure.
Operational Precision
Operational precision influences the quality of the final product. It is essential for achieving accurate angles and consistent bends.
- Tolerance Levels: Machines typically list tolerance ranges, which dictate how close the finished bend will be to the target specification.
- Measurement Tools: Some equipment comes integrated with measurement systems, enhancing accuracy.
Selecting equipment with high precision ratings minimizes rework and maximizes throughput in production environments.